迪恩机床
医疗器械解决方案
医疗行业
作为全球机加工市场的重要参与者,迪恩机床通过与众多医疗行业客户建立密切的关系和提供解决方案,支持医疗器械行业的发展。
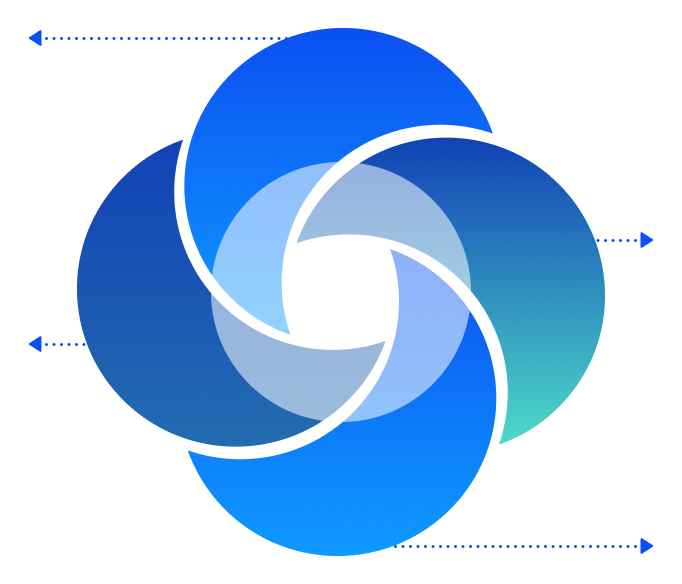
- 400 个型号 + 解决方案 提供针对各种复杂形状和条件进行优化的解决方案
基于我们强大的机床产品阵容和应用工程领域的专业知识,我们能够针对客户需求提供优化的解决方案。
- 遍布63个国家的162个销售网络
(51个全球技术中心) 建立密切的关系我们建立了快速响应系统,并与客户建立了密切的关系。
- 超过350个医疗器械客户 医疗器械行业多样化客户群的选择
各种医疗器械客户越来越多地选择迪恩机床来创造更高的收入。
- 研发人员占比 40% 对材料的深入了解
我们研发中心的许多研究人员基于他们对医疗器械材料的深刻了解,提供了出色的技术。
医疗器械解决方案参考
迪恩机床正在对众多医疗器械领域做出响应。
医用植入物
- 接骨螺钉
- 接骨板
- 人工关节
各种各样的医疗器械
各种医疗设备部件
接骨螺钉 : 生产接骨螺钉,需要根据精确的尺寸和形状对具有高强度和耐久性的各种材料进行高精度加工。
迪恩机床根据医疗器械客户的需求提供准确的解决方案。
接骨板 : 迪恩机床的解决方案用于加工接骨板,接骨板可通过使用接骨螺钉固定来稳定骨折或骨损伤。
人工关节 : 人工关节是替代患者关节的耐用结构,通过将昂贵的金属或陶瓷材料以高精度加工成复杂的形状造出。
迪恩机床提供的解决方案能够实现高水平的零件制造。
Workpiece Solution
-
牙种植体螺钉 牙种植体螺钉加工特点- 主要工件 : 钛
占地面积小可扩展自动化系统配置
出色的加工能力出色的加工能力 标准卡盘尺寸 型号 进给距离 mm 进给速度 m/min 功能 X轴 Z轴 X轴 Z轴 2轴 M MS 6英寸 Lynx 2100A / MA 205 340 30 36 ○ ○ − Lynx 2100LA / LMA / LMSA 560 ○ ○ ○ 8英寸 Lynx 2100B / MB 205 340 30 36 ○ ○ − Lynx 2100LB / LMB / LMSB 560 ○ ○ ○ 10英寸 Lynx 2100LC 205 560 30 36 ○ ○ ○ 卓越的加工性能 : Lynx 2100LB配备了15kW大功率电机,机床结构和主轴以及刚性增强的进给轴,使其具有出色的加工能力。
其最大加工直径为Ø350mm,最大加工长度为550mm。高可靠性 : 传与现有的型号相比,Lynx 2100LB具有宽支撑结构、稳定的床身结构和低振动/低噪声结构主轴,确保了高度的可靠性。
它还配有一个伺服刀塔和一个用于防止泄漏和切屑卡住的全封闭护罩,提高了性能和耐用性。 -
椎弓根螺纹件 椎弓根螺纹件加工特点- 主要工件 : 钛
复杂加工能力稳定的高刚性结构确保了精密加工- 所有轴均配有箱式导轨。
- 刚性加强主轴和支撑轴承确保了重型切削的精度。
高性能Y轴复杂加工- 使用Y轴在垂直、水平和横向上自由操纵旋转铣刀
-
小接骨板 小接骨板加工特点- 主要工件 : 钛
直联式主轴DNM 350/5AX配备直联式主轴,最大程度降低了噪音和振动,且只需一次装夹即可执行从高速加工到强力切削的所有操作。
最高主轴转速- 12000 r/min (DNM 350/5AX : 20000 r/min)
电机功率- 18.5 / 11kW
复杂加工能力高精度进给系统- DNM 350/5AX配备了滚柱式线性导轨和高刚性联轴器,可提高X、Y和Z轴直线进给系统的刚性和精度。
自动换刀装置自动换刀装置 分类 刀库容量(把) 换刀时间(秒)(T-T-T) DNM 200/5AX 30 (40) 1.3 DNM 350/5AX 30 (40, 60) 1.3 旋转工作台- 高刚性和高精度的A轴和C轴滚柱轴承
-
髋 - 股骨头 髋 - 股骨头加工特点- 主要工件 : 不锈钢,钴铬合金
出色的加工能力TT系列通过使用第二主轴和副刀塔,具有极高的生产率- 第一和第二主轴、上刀塔和下刀塔均可独立操作。
- 提供各种棒料加工直径(φ42 ~φ81mm)
- 带有Y轴的附加刀塔,用于上部和下部。
- 为第一和第二主轴部署完美的自动化装置。
加工速度快通过传输系统的优化技术提高刚性和力度- 40m/min的快速传输速度,可满足设备对高生产率的要求。
- 采用高刚性滚柱式线性导轨
第一主轴、第二主轴(8英寸) 最大功率- 22 / 15 kW
最高转速- 5000 r/min
-
髋 - 股骨柄 髋 - 股骨柄加工特点- 主要工件 : 不锈钢
复杂加工能力强大的复合加工能力,更高生产率- 第一和第二主轴、B轴、铣削和下刀塔的组合加工能力
- 通过正交结构,将加工范围最大化。
- 可选的12工位伺服刀塔可提供强大的切削功能。
高精密卓越控制能力,更高精密度- 实现对B轴和C轴的精度控制。
- 通过高速冷却装置和智能热位移校正功能,最大程度减少热位移。
第一主轴C轴位置控制能力- 0.0001°
-
人工关节 人工关节加工特点- 主要工件 : 不锈钢
复杂加工能力强大的复合加工能力,更高生产率- 第一和第二主轴、B轴、铣削和下刀塔的组合加工能力
- 通过正交结构,将加工范围最大化。
- 可选的12工位伺服刀塔可提供强大的切削功能。
高精密卓越控制能力,更高精密度- 实现对B轴和C轴的精度控制。
- 通过高速冷却装置和智能热位移校正功能,最大程度减少热位移。
第一主轴C轴位置控制能力- 0.0001°
-
锤子 锤子加工特点- 主要工件 : 不锈钢
出色的加工能力TT系列通过使用第二主轴和副刀塔,具有极高的生产率- 第一和第二主轴、上刀塔和下刀塔均可独立操作。
- 提供各种棒料加工直径(φ42 ~φ81mm)
- 带有Y轴的附加刀塔,用于上部和下部。
- 为第一和第二主轴部署完美的自动化装置。
出色的加工能力通过传输系统的优化技术提高刚性和力度- 40m/min的快速传输速度,可满足设备对高生产率的要求。
- 采用高刚性滚柱式线性导轨
第一主轴、第二主轴(8英寸) 最大功率- 22 / 15 kW
最高转速- 5000 r/min
迪恩机床的医疗器械行业客户
迪恩机床通过提供高质量的解决方案,忠实地响应全球医疗器械公司的各种需求。
150+ 100+ 100+
美洲
- 最大的市场,这里有各种不同的公司选择迪恩机床。
欧洲
- 建立以1~2级公司为重点的关系。
韩国/亚洲
- 从专注于韩国市场扩展到中国和东亚其他地区,跨国公司正在进入新的领域。