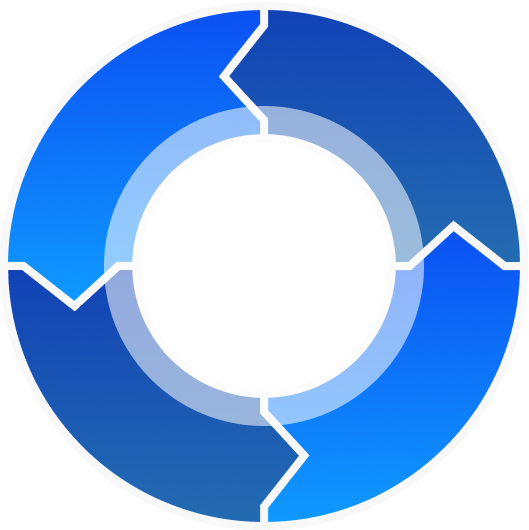
Operations
- Stepper
Exposure - Etching
- Diffusion
- Deposition
In the semiconductor industry, where extremely high precision and diverse and complex material machining are required to manufacture fine
structures, DN Solutions contributes to improving semiconductor quality and reliability by providing specialized solutions for each process.
DN Solutions always puts our customers first by providing them with unique solutions designed to produce the best results under all conditions.
Annually, DN Solutions supplies more than 80%* of machine tools which are consumed in Korean semiconductor equipment manufacturing market
DN Solutions offers optimal solutions for various materials from ceramics to difficult-to- machine materials such as stainless steels and titanium
We provide the best full-process service, ranging from pre-order qualification to on-time delivery with continuous consideration of customer needs, and comprehensive post-delivery services
Experience more efficient and optimized various lineup and workpieces by DN Solutions’ tailored solutions.
Vacuum Equipment :
DN Solutions provides various solutions for manufacturing vacuum equipment that require a very high level of precision.
Transfer Systems :
A transfer system is a system that precisely, quickly, and safely transfers wafers between various equipment and is one of the key elements of semiconductor manufacturing. DN Solutions provides various solutions for manufacturing Transfer System parts that require a very high level of precision.
Spraying/Cleaning/Heating
PUMA GT2100 | PUMA GT2600 | PUMA GT3100 | |
---|---|---|---|
Cutting speed | 270m/min | 270m/min | 280m/min |
Feedrate | 0.3mm/rev | 0.3mm/rev | 0.3mm/rev |
Spindle speed | 1131r/min | 1131r/min | 849r/min |
Cutting depth | 3mm | 3mm | 3mm |
Chip removal rate (cm³/min) | Spindle speed (r/min) | Feedrate | ||
---|---|---|---|---|
Face mill (Ø80mm) Carbon steel (SM45C) |
527 | 1500 | 2700 |
![]() |
Face mill (Ø80mm) Aluminium (AL6061) |
1901 | 1500 | 5490 |
![]() |
End mill (Ø30mm) Carbon steel (SM45C) |
48 | 222 | 107 |
![]() |
U-Drill (Ø50mm) Carbon steel (SM45C) |
501 | 1500 | 155 |
![]() |
Tap Carbon steel (SM45C) | Tap size (mm (inch)) M 36 x P 4.0 | 221 | 884 |
![]() |
Cutting Capacity(Unit : mm) |
![]() |
|||||
---|---|---|---|---|---|---|
Model | Max.tool diameter x Max.tool length | Tool change time(tool weight of less than 12 kg (26.5 lb)) | ||||
BT / CT / DIN | HSK | Model | Tool to tool | Chip to chip | ||
NHM 5000 | 320 x 530 | 320 x 600 | NHM 5000 | 2s | 6.4s | |
NHM 6300 | 320 x 630 | 320 x 700 | NHM 6300 | 6.7s | ||
NHM 8000 | 320 x 630 | 320 x 700 | NHM 8000 | 8s |
Realizes high-quality, high-precision machining with smoothing thermal displacement compensation of the spindle and structure.
Thermal analysis of the symmetrical structure proves that this is the optimal solution for high precision machining of mild materials.
Adopting a new constant preloading structure, improved spindle rigidity in low-speed range and achieved long spindle life.
20000 r/min | 15000 r/min | 30000 r/min | 30000 r/min | |
---|---|---|---|---|
spindle motor power (kW) | 22/11 | 37/22 | 18.5/13 | 5.5/3.7 |
공구 규격 | BBT 40 | BBT 40 | HSK-F63 | HSK-E40 |
Chip removal rate (cm³/min) | Spindle speed (r/min) | Feedrate | ||
---|---|---|---|---|
Face mill (ø80 mm, number of flutes: 6) Carbon steel (SM45C) |
374.4 | 500 | 1950 |
![]() |
Drill (ø50 mm) Carbon steel (SM45C) |
265.07 | 500 | 135 |
![]() |
Tap Carbon steel (SM45C) | Tap size (mm (inch)) M 36 x P 4.0 | 265 | 1060 |
![]() |
DN Solutions is helping the Korean semiconductor industry contribute to the world by providing the technology, knowledge and solutions required by the
Korean IT industry.
Supplied to Korean IT
industry for
2 years
Market share in Korean
IT Industry
Companies using parts
which is manufactured by
DN Solutions machine
Among the Top20